If you work in the pharmaceutical or medical device industry, you know that problems will pop up, it’s just a reality of manufacturing and compliance. The key isn’t to avoid issues altogether (that’s impossible), but to catch them early, fix them properly, and prevent them from happening again. That’s exactly what a Corrective and Preventive Action (CAPA) system is designed to do.
A well-run CAPA system isn’t just about staying compliant with regulations; it’s about protecting your customers, improving efficiency, and keeping your business running smoothly. But let’s be honest—CAPA can feel overwhelming, especially if you don’t have a clear process in place. Whether you’re a small startup or a large organization, here’s how to build a system that actually works.

Start with a Clear Process
One of the biggest CAPA mistakes companies make is treating it like a box to check instead of a structured problem-solving tool. Without a clear process, issues get overlooked, fixes are rushed, and the same problems keep coming back.
A strong CAPA system starts with defining when to open a CAPA. Is it triggered by customer complaints? Audit findings? Equipment failures? Setting clear guidelines will ensure your team knows when and how to act. Just as important is assigning responsibility—who investigates, who takes action, and who ensures the problem is truly resolved? CAPAs can drag on for months without clear ownership, so having defined roles keeps things moving.
Fix the Real Problem, Not Just the Symptoms
A common pitfall is addressing surface-level issues without digging deeper to find the real cause. Imagine a company repeatedly dealing with a contamination issue on its production line. If they just clean the area and move on, the problem will keep coming back. But if they investigate further, they might discover that an air filter isn’t being replaced as often as it should be. That’s the real issue, and fixing it prevents future problems.
Root cause analysis is the key to making CAPA effective. Tools like the 5 Whys method (asking "why" multiple times to drill down into the cause) or a fishbone diagram (which maps out all possible contributing factors) can help teams uncover what’s really going wrong. The goal isn’t just to put out fires—it’s to figure out what’s fueling them in the first place.
Make Sure the Fix Actually Works
Once the root cause is identified, the next step is putting corrective actions in place. This might mean updating a process, retraining employees, switching suppliers, or even modifying a product design. But implementing a fix isn’t enough, you need to verify that it’s actually working.
Too often, companies assume that once an action is taken, the problem is solved. But without a follow-up plan, there’s no way to know if the fix is effective. Setting a timeline for reviewing and gathering data on whether the issue recurs can help ensure the corrective action is doing its job.
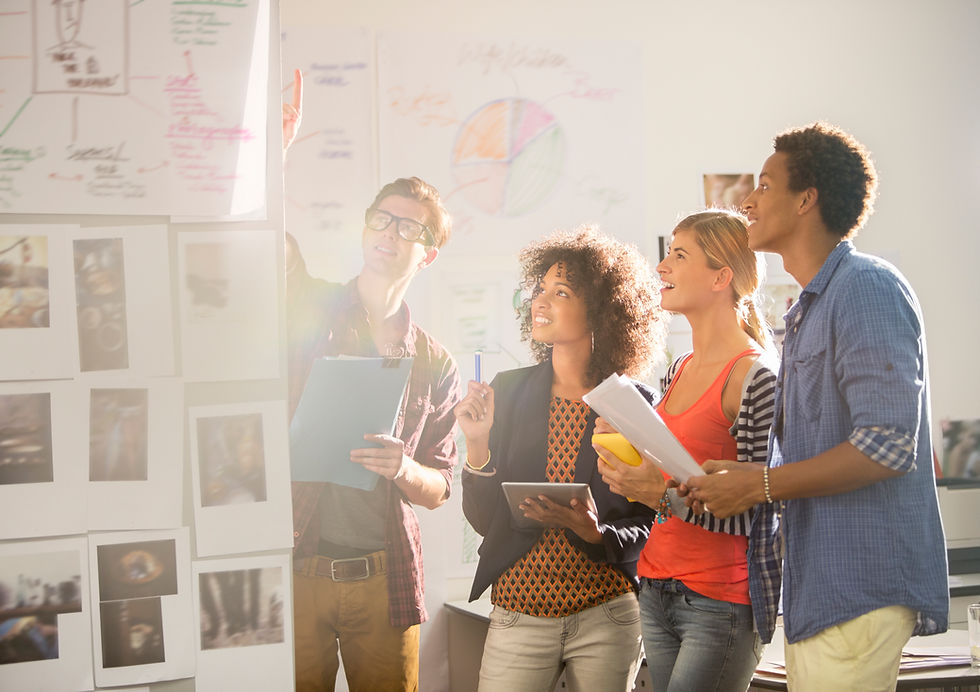
Think Prevention, Not Just Correction
The best CAPA systems don’t just react to problems, they prevent them from happening in the first place. This means looking for patterns and trends across different issues. If multiple CAPAs point to a training gap, for example, then addressing that gap proactively can prevent future nonconformances.
Encouraging employees to speak up about small issues before they escalate also plays a big role. A culture where employees feel comfortable raising concerns helps catch problems early—before they require a full-blown CAPA investigation.
Good Documentation Makes Audits Easier
If there’s one thing that will make a regulatory audit smoother, it’s solid documentation. CAPA records should tell a complete story: what the issue was, what caused it, what was done to fix it, and how the company ensured the problem wouldn’t happen again.
When records are incomplete or disorganized, it raises red flags for auditors. On the other hand, when a company can easily show how it handled past issues, it demonstrates a strong commitment to quality and compliance.
Final Thoughts on CAPA

A CAPA system isn’t just about meeting FDA or ISO requirements, it’s about improving your business and keeping customers safe. When done right, it helps identify weaknesses, drive continuous improvement, and prevent costly mistakes.
The key is to keep it structured, proactive, and focused on real solutions. If your CAPA process feels like a burden instead of a tool for improvement, it may be time to rethink how it’s implemented. And if you’re not sure where to start, reach out or click the button below. We’d be happy to help.
Commenti